FINoak prefinished oak flooring is a versatile solution for homes, offices, and retails spaces. With the introduction of both prefinished and unfinished flooring options available you need to make sure you choose the right product for your application. Let’s unpack the benefits of prefinished flooring.
Before we can get to the surface and finishes, we need to examine the product.
What is engineered wood?
Engineered wood is manmade.
It is a hardwood board that is manufactured from multiple layers of material bonded together and an oak wood veneer (thin slice of hardwood) top face.
Each layer in the core run in perpendicular directions creating increased dimensional stability and prevent the wood from expanding or contracting that cause warping and bowing in humid or dry areas, in the way a solid hardwood might react.
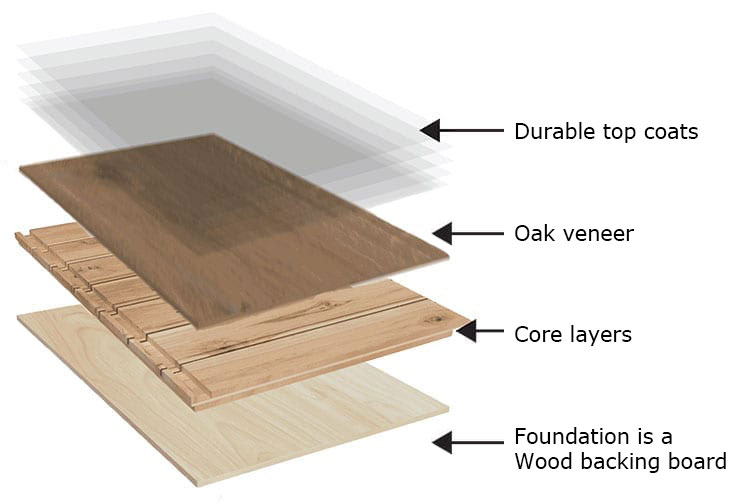
Engineered wood is environmentally friendly
It requires the cutting down of fewer trees, creates less waste and has greater product yielded from precious and costly hardwoods. Engineered versions of hardwood flooring are less expensive and easier to source.
Greater Versatility
Engineered wood floors can be installed on and over a variety of sub-floors and installed by either a floating click system or full bonded glue down installation and don’t need to be nailed to the floor.
Easy installation
The Installation of prefinished hardwood flooring is quick and easy when compared to unfinished floors. Finoak pre-finished oak flooring is already coated in a factory setting, and does not need to be sanded and finished on-site, which eliminates the need to put up with the noise, dust and toxic smells that go along with installation of unfinished flooring.
Thereby saving you time, money and inconvenience. Prefinished floors can furthermore be walked on immediately and have no curing time.
Non Toxic
Installation of prefinished flooring means less mess and noise, as well as ZERO toxins and unpleasant smells that are unavoidable when traditional flooring is finished on-site. This is a major advantage for highly trafficked areas, or households with pets, children, or people with allergies. Prefinished hardwood flooring is a hypo-allergenic flooring solution.
Durability
Prefinished flooring runs through the finishing production line several times and has multiple coats of finish and strengtheners applied using a UV-curing technology in a strictly-controlled factory setting. This makes the wear layer of prefinished hardwood flooring very resilient, and the finish itself comes under manufacturer warranty, which is substantially better than any contractor warranty applied in the field. Unique finishing technologies(Smoked) and drying conditions that are available at an industrial plant are simply impossible to replicate on-site. Factory applied finishes are more abrasion resistant and are free of dust, brush hairs and swirl marks. These evenly applied heavy duty finishes do not have an odour. While site-finished floors last 3-5 years (6-maximum) before needing to be refinished, most prefinished floors can last for decades.
Natural wood texture and unique coloring techniques
Factory applied finishes tend to be highly transparent, which allows to preserves the look of the natural wood texture and depth of colour to the maximum. Factory prefinished hardwood floors are available in a wide range of colours, surface finishes and styles.
15/4 Pre-finshed (190 x 1900 x 15/4mm)
14/3 Pre-finished (260 x 1900 x 14/3mm)
Tsitsikama
Production process:
Brushed, Light, White Oiled, White Wax Oiled. This product is dried naturally, and the Smoked veneer is fumigated in a closed smoke kiln. The color of the smoke permeates the whole veneer, making it more natural, and the other processes are dried naturally. Each process takes 1-2 days to dry naturally.
Sugarbush
Production process:
Brushed, Dark smoked, White Washed and White Wax Oiled. This product is dried naturally, and the Smoked veneer is fumigated in a closed smoke kiln. The color of the smoke permeates the whole veneer, making it more natural, and the other processes are dried naturally. Each process takes 1-2 days to dry naturally.
Warranties
Warranties vary on engineered wood depending on the grade of the wood and the wood species. Domestic woods, such as maple and oak might come with a 10 to 20 year warranty. All FINoak product come with a 25 year manufacturer’s warranty.
In general, engineered wood can be put throughout the house, requires less maintenance, is more moisture resistant, and generally at a lower cost – making it a popular flooring solution.